Energy-related projects added spice to CSC classes
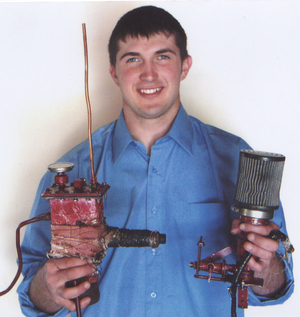
A couple of energy-related projects added spice to the regular curriculum for industrial technology students at Chadron State College during the 2006 spring semester.
One involved building and testing a device that is intended to improve the fuel efficiency of gasoline engines and the second was construction of a 500-watt wind turbine to produce electricity.
While neither project is ready for consumer use, both appear to have possibilities and are worthy of future exploration, according to Kevin Miller, assistant professor of industrial technology at CSC.
“Both project provided special interest among the students as they saw how the numerous hours of classroom experiences they have had can be applied to make devices that may be applicable to their lives,” said Miller. “I think everyone involved learned quite a bit and enjoyed trying to solve the problems they ran into.”
The gasoline efficiency project got its start when Gerald Rowley, an inventor in Florida, contacted Miller after learning about the High Mileage Contest that the Industrial Technology Department hosts during the High School Scholastic Contest at CSC each spring.
Rowley was interested in having CSC students construct and test his Vapster fuel vaporization device that he believes can improve the mileage of motor vehicles by up to 40 percent.
Ben Morse, a senior from Sargent, agreed to tackle the project. It included procuring the materials needed to build the Vapster and testing it. During the several weeks that Morse worked on the project he often communicated with Rowley by phone or email to trade information.
The inventor’s idea is to gravity feed fuel into a stainless steel chamber that will sit atop the engine. The chamber is heated by the engine exhaust to about 325 degrees Fahrenheit, vaporizing the fuel before it enters the engine and making it burn more efficiently. A battery-operated pump forces the fuel through a small carburetor and into the cylinder heads.
Morse took the Vapster home with him during spring break and had it working on a 5-horsepower engine. When he returned to Chadron, he placed it on a 3-horsepower engine, but the Vapster overheated and the engine was damaged. He believes the second engine was too small and also speculated that the higher altitude in Chadron may have contributed to the problem.
Morse graduated in May, but is not giving up on the project. He took the materials home with him and plans to continue working on it.
“It’s going to be a trial and error process and it’s going to take a lot of time,” said Morse. “But I’ll make it work. I had the Vapster I had made converting gas into vapor. It’s got possibilities. I’ll be working at the golf course at Sargent this summer and will have some opportunities to experiment with it.”
During the reception a few minutes after he’d graduated, Morse and his father were discussing what engines they possess would work best for the next trial run.
Meanwhile, Rowley has informed Miller and Morse that Dodge Motor Co. has expressed interest in becoming involved in developing the Vapster for possible use on its sports utility vehicles.
Eleven students in two advanced electronics classes formed a team to build a wind turbine after Miller got the idea while attending an energy-related workshop in Fort Collins, Colo., last fall.
Since the students started from scratch, the construction phase was not simple. Again, many hours of tedious work were involved. The spring 2006 Industrial Technology Department’s newsletter described the process in detail.
The stator, where the electrical charge is produced by the whirling blades, is composed of nine windings made of No. 17 wire to form the coils that are encased in fiberglass resin to protect them.
Two rotors were attached to a trailer spindle, the hub and the blade assembly. Each rotor was made of a 12-inch diameter plate of three-eighths inch steel. Twelve powerful ceramic magnets are attached to the rotors with “super glue” and surrounded with fiberglass resin for protection.
Miller said the wooden blades to catch the wind were some of the most difficult parts to build. Made of redwood, they began as 2x8s that were ripped into 2x2s and then glued back together to form stronger, laminated structures.
The blades were shaped by using a band saw, hand planer and sanders to form shapes similar to an airplane propeller. The students added a special touch when they designed the tail to resemble the eagle that is used as the CSC athletic teams’ mascot.
The estimated cost of all the materials was about $700. The similar commercially-produced turbine costs several thousand dollars, but the CSC students learned that the construction involves lots of work.
After the turbine was completed it was displayed in late March at the Alternative Energy Conference in Ainsworth, where it drew many questions, particularly on the construction process and how much electricity it might produce.
The semester ended before the completed turbine could be tested. Miller said a rectifier must be built to covert the 48 volts of three-phase power into 48 volts of direct current.
Since Miller will be taking a sabbatical this fall to complete work on his doctorate, he said completing the project will probably have to wait at least until next spring.
The CSC professor said an apparatus similar to the one built at CSC this spring might be suitable as an alternative energy source or to operate a submersible pump for watering livestock, but much more energy is needed to satisfy the average American.
Miller said the wind turbine should produce one kilowatt in a 21 mph wind, but at least 30 kilowatts are needed to completely supply a typical home with electricity.
Category: Campus News